一、随着科学技术的飞速发展,在航空、电子、计算机、模具制造等领域,对精密机械零件的工艺性能要求不断完善,零件的不断小型化,表面质量及功能性边缘、边角要求的不断提高,致使目前用手工,化学等传统的加工工艺方法对零件表面及其内部进行抛光,倒角及去毛刺均有其局限性,特别是对零件内小孔径相互交叉的孔径及边棱进行抛光,倒角去毛刺是无能为力的。

由此,一种全新概念的经济有效的自动化光整加工技术——磨粒流加工技术 (又称挤压、研磨技术)应运而生。磨粒流,是指一种抛光去毛刺工艺,又称为流体抛光,或挤压研磨抛光,主要针对内孔、微细孔、不规则形状、球面曲面、齿轮等,以效率高、抛光去毛刺彻底、不伤工件而著称。简单来说,就是通过半流体介质进行抛光去毛刺的工艺,主要面向内孔、以及不规则形状的中小型工件。
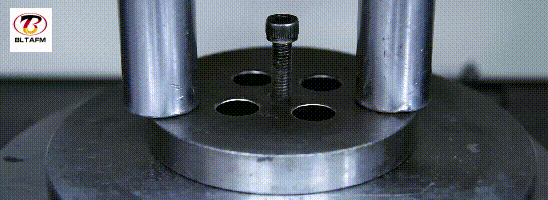
AFM磨粒流,不只是设备,而是一项全力整合的系统系工程。
二、磨粒流的加工原理:
是通过一种挤压方法,其磨料具有流动性,其中的颗粒不断地对工件表面进行研磨,完成抛光和去毛刺加工。
磨粒流磨膏,是由一种具有粘弹性、柔软性和切割性的半固态载体和一定量磨砂搅而形成。不同载体的粘度、磨砂种类、磨粒大小,可以产生不同的效果。磨料依加工物的形状、材质、加工目的有各种不同的规格。
规格是依载体的粘弹度、砂粒、材质、粒度的组合来做调合。一般是在铸铁、铝、铁加入常碳化硅作为标准的磨料。如用于超硬或陶瓷则使用钻石磨料。
高粘度磨料可用于对零件的壁面和大通道进行均匀研磨;低粘度磨料用于对零部件边角倒圆和小通道进行研磨磨粒流,磨料的流动性和砂粒的切削能力,使磨粒流成为一把游动的去毛刺工具。

三、磨粒流的三大核心技术:
1、 磨料配方:这几乎是每家企业的核心机密,每家企业的配方都不一样,所以抛光效果也不尽相同;
软磨料是由非常细小的硬质颗粒,混合相关液体,调制而成的半流体状态的介质,磨料颗粒的大小、硬度,以及半流体的黏稠度、遇热后是否会黏贴工件,是影响抛光去毛刺质量的关键。磨料通常选材有碳化硅、白刚玉、金刚石等,根据各自的硬度,对应不同材质的工件。例如铝制品、铜制品工件,选用碳化硅磨料即可。而硬度较高的钨钢、合金钢,选用白刚玉或金刚石更为合适。
2、 工装夹具:工装夹具设计的好坏,直接决定了抛光效果的稳定性、效率性,以及操作的简便性。
选用工装夹具的原因是,为了提高工件抛光去毛刺的效率。一来,一款夹具上可以同时夹持多个工件,一次性加工。二来,使用工装夹具后,退模换工件时,不必每次校准,大大减少了停机时间。
工装夹具设计的关键在于,在提升效率的前提下,如何保持工件均匀受力,而不致于使工件压伤。
3、 PLC系统:PLC系统是整个磨粒流设备的控制中心,PLC系统设计简洁、规范,既可以让操作人员更快上手,减少培训磨合时间,又可以减少设备故障率,延长设备使用寿命。

四、磨粒流工艺的优缺点:
1、磨粒流工艺的优点在于:处理内孔以及不规则形状的工件抛光时,有着极为优异的表现,效率高、效果好;
2、磨粒流工艺的缺点在于:无法处理尺寸较大的工件,不适合进行平面抛光,不适合处理圆管外壁。